Blog
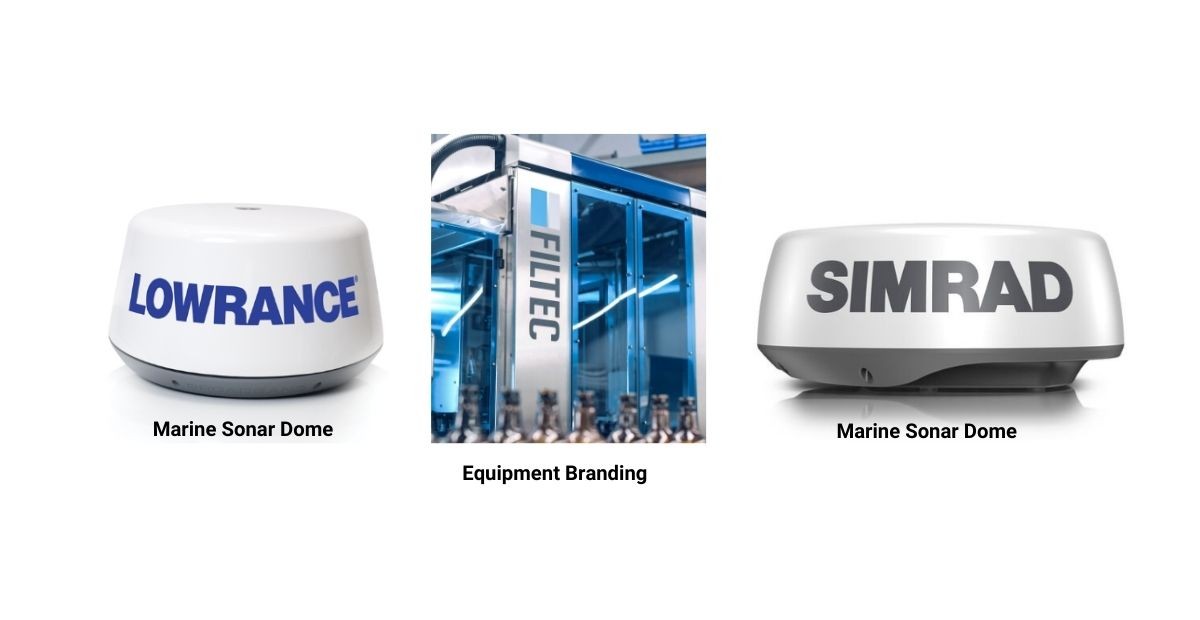
Enhancing Industrial Operations with Pressure Sensitive Vinyl Decals: Benefits, Features, and Applications
Posted: August 29, 2024 |
Maximizing Efficiency and Durability with Pressure Sensitive Vinyl Decals in
Industrial Manufacturing
In the realm of industrial manufacturing, the importance of effective labeling cannot be overstated. Pressure sensitive vinyl decals, often overlooked, offer a versatile, durable, and cost-effective solution that can significantly enhance operational efficiency and product presentation. This article explores the benefits, features, and applications of pressure sensitive vinyl decals.
Understanding Pressure Sensitive Vinyl Decals
Pressure sensitive vinyl decals are adhesive-backed labels made from a thin, flexible plastic film. The term "pressure sensitive" indicates that these decals adhere to surfaces with minimal pressure, eliminating the need for heat, water, or solvents. Despite their simplicity, these decals are engineered to deliver exceptional performance in various industrial applications.
Benefits for Industrial Manufacturers
Industrial manufacturers stand to gain numerous advantages from utilizing pressure sensitive vinyl decals:
- Durability: These decals are designed to withstand harsh environments, including exposure to chemicals, UV rays, and extreme temperatures, making them ideal for industrial settings.
- Versatility: Pressure sensitive vinyl decals can be used for a wide range of purposes, from product identification and safety warnings to branding and operational instructions.
- Ease of Application: The application process is straightforward and efficient, reducing downtime and labor costs.
- Customization: Manufacturers can specify the size, shape, and color of the decals to meet their exact requirements.
- Compliance: These decals can help manufacturers meet industry-specific labeling requirements for safety and regulatory compliance.
Engineering Excellence Behind the Decals
The adhesive technology used in pressure sensitive vinyl decals is a testament to modern chemical engineering. It creates a strong bond with minimal pressure and can be tailored for either permanent or removable applications. The vinyl material itself is engineered to resist tearing, shrinking, and fading, even under challenging industrial conditions. Certain types of vinyl can also withstand exposure to acids, solvents, and other harsh chemicals.
Practical Applications in Industrial Manufacturing
Pressure sensitive vinyl decals are highly practical for various industrial applications:
- Equipment Labeling: Durable and legible labels for machines, tools, and parts.
- Safety Signage: Clear and visible safety warnings that remain intact over time.
- Product Branding: Logos and product information directly applied to manufactured goods.
- Inventory Management: Color-coded or barcode labels to streamline inventory processes.
- Instructional Labels: Operating instructions affixed directly to equipment.
The Advantage of Pre-Masked Applications
For complex designs or large decals, pre-masked applications offer significant benefits. Pre-masking involves applying a transfer tape over the decal, ensuring all elements remain perfectly aligned during application. This technique is particularly useful for multi-color designs or intricate shapes, facilitating easier and more precise installation.
Selecting the Appropriate Decal
Choosing the right pressure sensitive vinyl decal involves considering several factors:
- Surface Type: Different surfaces (smooth, textured, flat, curved) require different adhesive strengths.
- Environmental Conditions: Decals exposed to extreme temperatures, UV rays, or chemicals need to be made from suitable materials.
- Duration: The intended lifespan of the decal (short-term or long-term) will determine the grade of vinyl required.
- Removability: Depending on whether the decal needs to be removable or permanent, the adhesive properties must be selected accordingly.
Installation Best Practices
Proper installation is crucial for the performance of pressure sensitive vinyl decals. Here are some best practices:
- Surface Preparation: Ensure the surface is clean and free from dirt, oil, or residue.
- Temperature Control: Apply decals in a temperature-controlled environment, ideally between 50-80°F (10-27°C).
- Application Tools: Use a squeegee or roller to apply even pressure and eliminate air bubbles.
- Hinge Method: For large decals, apply one edge first and gradually smooth down the rest to ensure proper alignment.
Pressure sensitive vinyl decals represent a small yet impactful detail in the industrial manufacturing process. Their durability, versatility, and cost-effectiveness make them an excellent choice for a wide range of applications. By selecting the appropriate decal and following best practices for installation, manufacturers can enhance their operational efficiency and product presentation.
In the competitive landscape of industrial manufacturing, attention to detail can make a significant difference. Pressure sensitive vinyl decals offer a reliable and efficient solution for various labeling needs, ensuring that manufacturers can meet both functional and regulatory requirements with ease.
If you are looking to get started, Steven Label is here to provide expert guidance and support. Reach out to us today for a free consultation. We can guide you through all the options of pressure sensitive vinyl decals, demonstrating how they can enhance your product.