Blog
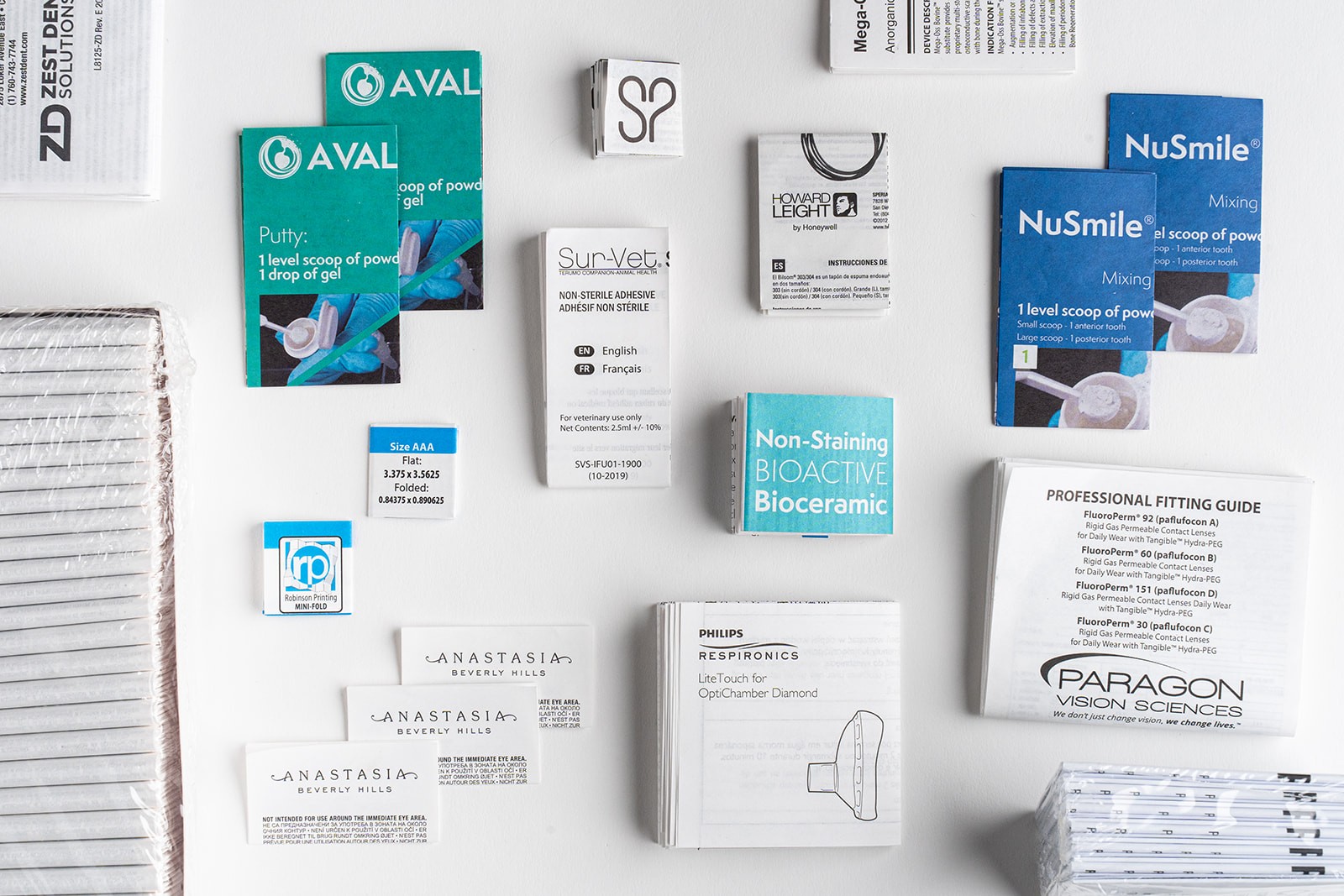
How to Write Effective Specifications for IFUs, Inserts and Outserts
Posted: February 28, 2025 |
In the wake of COVID-19 and the resulting supply chain disruptions, it became clear that flexibility in specifications can significantly impact a product’s continuity in the market. Companies with adaptable specifications managed to keep production running smoothly, while those with more restrictive specs faced significant challenges. Crafting well-balanced, flexible specifications for Instructions for Use (IFUs), Inserts, and Outserts is essential for minimizing disruption and ensuring continuous delivery. We will discuss insights and best practices to help you develop effective specifications for your printed materials.
Collaborate Early with Your Print Vendor
The first step in developing a reliable specification is to engage your print vendor before beginning the process. A print vendor’s expertise in sourcing, materials, and manufacturing can be invaluable in helping you avoid overly narrow specifications, which could lead to delays should supply chain issues arise. By collaborating with your vendor early, you can work together to ensure that your specs are adaptable and well-suited for both current and future needs.
Benefits of Broad Yet Specific Material Descriptions
One common area where specifications can be made more flexible is in the choice of materials. During the COVID-19 pandemic, we saw firsthand how narrow material specs could lead to major bottlenecks. For instance, specifying a particular brand of paper, instead of a generic description, restricts the vendor's options and may lead to sourcing issues if that brand becomes unavailable. Instead of calling out a specific brand, consider using general terms such as “27 lb opaque offset.” or a “GSM paper thickness”. This way, the vendor has more freedom to source compatible paper types without compromising on quality or specifications.
Qualifying Multiple Material Options for Security
For added assurance, you might consider qualifying two closely related options, such as 27 lb and 30 lb opaque offset paper. The slight difference in thickness is often imperceptible in the finished product, and having multiple options approved can ensure your project’s continuity even if one material becomes unavailable. For most IFU and label applications, this level of flexibility will have little to no impact on the appearance and functionality of the final product. Including this type of flexibility within your approved specifications can be a lifesaver during paper shortages or supply chain challenges, ensuring that production timelines stay on track.
The Impact of Adhesive and Material Shortages
During the pandemic, the industry faced a massive adhesive shortage that impacted companies across sectors. Businesses with broader specifications were able to pivot to alternative materials quickly, whereas those with narrow specifications encountered significant delays due to the need to requalify different adhesives. In some cases, companies were unable to place orders until the preferred materials became available again. By building flexibility into your adhesive and substrate specifications, you can mitigate the risk of material unavailability and ensure uninterrupted production.
While flexibility is essential, overly broad specifications can also present challenges. In some cases, if specifications lack precise details, you may receive materials that don’t meet functional requirements. For example, if your IFU’s paper specification only mentions paper weight without considering fold characteristics, you could end up with an overly thick insert that doesn’t fit neatly into your package. Similarly, if a label’s specifications don’t specify a particular laminate, you may receive labels that degrade quickly when exposed to moisture or extreme temperatures. Ensuring that your specifications are neither too narrow nor too broad requires careful attention and a partnership with your print vendor to strike the right balance.
Practical Steps for Creating Robust Specifications
Step 1: Start with a Vendor Consultation
Before drafting your specifications, consult with your vendor. They can offer insights on material availability, sourcing challenges, and alternative options that align with your quality standards. This step is crucial for creating adaptable specifications that won’t compromise the durability or function of your printed materials.
Step 2: Use Generic Descriptions When Possible
Avoid specifying brand names and instead use general descriptions of materials and substrates. Using terms like “27 lb opaque offset” or “adhesive suitable for cold storage” broadens your options and prevents supply issues related to specific brands or proprietary materials.
Step 3: Approve Multiple Material Options
During the packaging validation phase, consider qualifying more than one material option. For instance, you might validate both 27 lb and 30 lb opaque paper, or approve two adhesives that meet your functional requirements. This approach gives your vendor flexibility to choose the best material available at any given time, which can be critical in times of supply chain stress.
Step 4: Balance Flexibility with Precision
While flexibility is important, ensure that your specifications provide enough detail to avoid unintended consequences. For example, if your label specs don’t specify a moisture-resistant laminate, you may receive labels that become illegible when exposed to cleaning solutions or refrigeration. Partnering with your vendor to identify which aspects of the specification can be flexible and which need precision will protect your product’s quality.
Conclusion: Ensuring Success with Balanced Specifications
Creating adaptable specifications is essential in today’s unpredictable market. By consulting with your print vendor, using generic terms, approving multiple options, and balancing flexibility with precision, you can better prepare your products for unforeseen disruptions. Taking these proactive steps not only ensures timely production but also helps you meet compliance requirements and maintain high standards of quality. Reach out Steven Label to discuss these best practices further, and learn how we can help optimize your specifications for greater supply chain resilience.